1. 30 MW Steam Turbine Project by GES
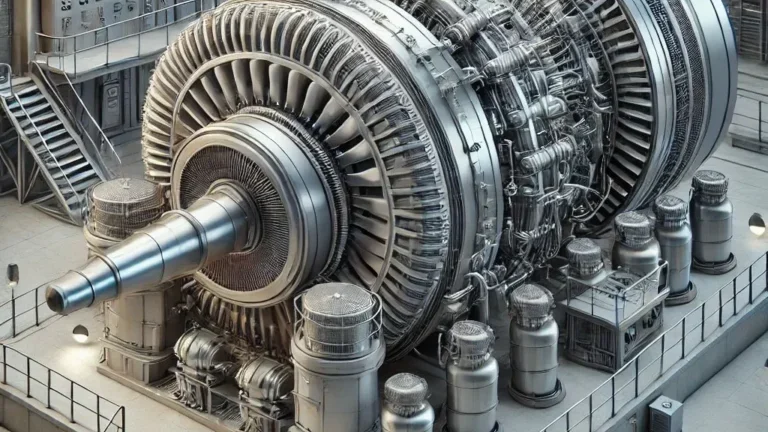
Overview
GES undertook the challenging task of designing, analyzing, and optimizing a 30 MW steam turbine to meet the specific needs of our client in the energy sector. This project required a combination of mechanical expertise, advanced simulation techniques, and seamless teamwork to deliver a high-performing solution within the stipulated timeframe and budget.
Project Objectives
- Design a steam turbine capable of generating 30 MW of power efficiently.
- Ensure compliance with industry standards and safety regulations.
- Optimize the turbine for minimal maintenance and maximum lifecycle.
- Deliver the project within a strict timeline.
Challenges Faced
- Complex Thermal Analysis: Accurately modeling the thermal expansion and heat dissipation across the turbine components.
- Material Selection: Identifying materials capable of withstanding high pressure and temperature while maintaining durability.
- Precision in Manufacturing: Ensuring that turbine components met exact tolerances for smooth operation.
- Tight Deadline: Managing design, analysis, and manufacturing phases within the agreed project timeline.
- Coordination Among Teams: Ensuring effective communication between design, simulation, and manufacturing teams.
Solutions Implemented
- Advanced Simulation Tools: Utilized tools like ANSYS and SolidWorks Simulation for thermal and structural analysis. This ensured the design could handle extreme operational conditions.
- Collaborative Design Approach: Conducted regular brainstorming sessions with multidisciplinary teams to refine designs and address technical issues.
- Material Testing and Selection: Conducted rigorous testing of materials to finalize the best options for blades, rotors, and casings.
- Quality Assurance Processes: Implemented stringent quality checks during manufacturing to maintain precision and reliability.
- Efficient Project Management: Adopted an agile project management methodology to ensure timely completion of all phases while addressing challenges dynamically.
Project Outcomes
- Delivered a fully functional 30 MW steam turbine that met all performance benchmarks.
- Achieved an efficiency improvement of 5% over initial estimates through design optimizations.
- Successfully completed the project within the agreed timeline and budget.
- Enhanced client satisfaction by providing detailed documentation and after-sales support.
Key Takeaways
- Innovation through Collaboration: Teamwork and regular communication were critical in overcoming design and production challenges.
- Importance of Simulation: Advanced analysis tools significantly reduced errors and iterations during the design phase.
- Adaptability: Flexibility in project management helped address unforeseen issues without impacting the timeline.
Conclusion
This project showcased GES’s capability to deliver high-performance mechanical systems under challenging conditions. Our team’s dedication and expertise were instrumental in ensuring the success of the 30 MW steam turbine project, further solidifying our position as a trusted partner in mechanical design and engineering solutions.
2. In-House Jig and Fixture Design by GES
Introduction
GES, a leading provider of mechanical design services since 2011, takes pride in its ability to handle complex projects in-house. This case study highlights our expertise in designing and manufacturing jigs and fixtures, showcasing the challenges faced, solutions implemented, and the importance of teamwork and design review in achieving superior outcomes.
The Project
A client approached GES with a requirement for custom jigs and fixtures to optimize their production line. The project involved creating robust, precise, and easy-to-use fixtures that would improve manufacturing efficiency and ensure product quality.
Challenges Faced
1. Complex Design Requirements:
- The fixtures had to accommodate diverse product dimensions without compromising precision.
- Ensuring ergonomic usability while maintaining high structural integrity was critical.
2. Material Selection:
- Choosing materials that offered durability and resistance to wear and tear while being cost-effective posed a challenge.
3. Tight Deadlines:
- The project required quick turnaround times to avoid delays in the client’s production schedule.
4. Manufacturing Feasibility:
- Ensuring that the design could be manufactured using available resources without compromising quality.
Solutions Implemented
1. Collaborative Design Approach:
- Our team conducted multiple brainstorming sessions to ensure all perspectives and ideas were considered.
- Design iterations were reviewed using advanced CAD tools like SolidWorks and Creo to refine the concepts.
2. Prototyping and Testing:
- We developed rapid prototypes to test the functionality and ergonomics of the designs before full-scale production.
3. Material Optimization:
- After thorough analysis, we selected materials that balanced durability and cost-effectiveness, ensuring long-term usability.
4. Efficient Workflow Management:
- A clear project timeline with milestones was established to track progress and address issues proactively.
Teamwork and Design Review
Our team’s collaborative spirit was pivotal in overcoming challenges. Weekly review meetings ensured:
– Consistent alignment with project goals.
– Immediate identification and resolution of potential issues.
– Incorporation of client feedback to meet their specific requirements.
Outcome
The project was successfully completed within the stipulated timeline, delivering:
– Highly precise and durable jigs and fixtures.
– Improved efficiency and quality in the client’s production processes.
– Positive client feedback, reinforcing GES’s reputation for excellence.
Conclusion
This case study underscores GES’s commitment to tackling challenges head-on with innovative solutions, teamwork, and meticulous design reviews. Our ability to execute complex jig and fixture projects in-house highlights our capabilities and dedication to delivering value to our clients.
3. Wind Turbine Tower Design by GES
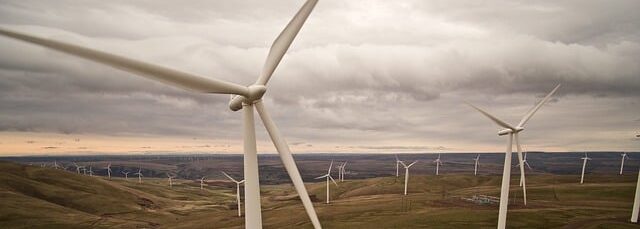
Overview
GES successfully executed the design, analysis, and optimization of a wind turbine tower for a leading renewable energy client. This project demanded innovative structural design, rigorous testing, and close coordination across teams to deliver a tower that is robust, efficient, and sustainable.
Project Objectives
1. Design a wind turbine tower that can support a 3 MW turbine under varying wind loads.
2. Ensure structural stability and safety in compliance with international standards.
3. Optimize the design for cost-effective manufacturing and installation.
4. Deliver the project within the client’s timeline and budget constraints.
Challenges Faced
1. Dynamic Load Analysis: Addressing varying wind loads, including gusts and turbulence, to ensure structural stability.
2. Material Optimization: Selecting lightweight yet durable materials to reduce costs without compromising strength.
3. Transportation and Installation: Designing a modular structure for easy transport and assembly at remote locations.
4. Environmental Considerations: Ensuring minimal environmental impact during construction and operation.
5. Tight Deadline: Coordinating between design, testing, and manufacturing within a strict schedule.
Solutions Implemented
1. Advanced Structural Analysis: Leveraged tools like ANSYS and Creo to model wind loads and optimize the tower’s structure for safety and efficiency.
2. Innovative Material Choices: Conducted extensive research and testing to finalize a combination of high-strength steel and composite materials.
3. Modular Design Approach: Designed the tower in modular sections for ease of transportation and on-site assembly.
4. Sustainability Measures: Incorporated eco-friendly construction practices and materials to minimize the project’s environmental footprint.
5. Efficient Team Collaboration: Adopted an agile methodology to ensure smooth coordination across all phases of the project.
Project Outcomes
1. Delivered a wind turbine tower capable of withstanding extreme wind conditions while supporting a 3 MW turbine.
2. Reduced material costs by 10% through innovative design and material selection.
3. Completed the project within the agreed timeline and budget.
4. Enhanced client satisfaction by providing comprehensive documentation and post-installation support.
Key Takeaways
– Importance of Load Analysis: Accurate simulation of wind loads was critical to ensuring the tower’s stability and longevity.
– Material Efficiency: The use of advanced materials contributed to cost savings and structural performance.
– Collaborative Success: Effective teamwork and communication played a vital role in addressing challenges and meeting project goals.
Conclusion
This project highlighted GES’s expertise in designing sustainable and efficient structures for renewable energy applications. The successful completion of the wind turbine tower project underscores our commitment to delivering innovative engineering solutions that meet client needs and environmental goals.